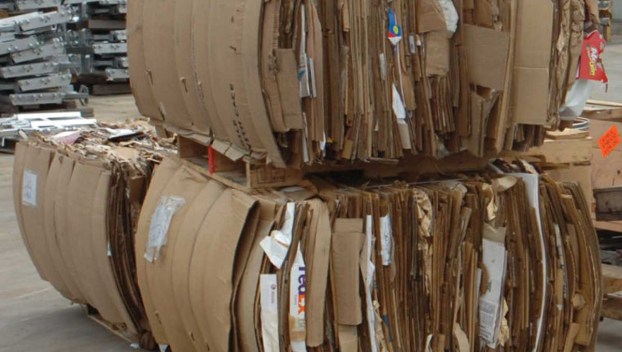
News
Recycling Reaches Companies Bottom Line
Energy Absorption Systems, LLC in Pell City has saved over $136,000 in the past eight months by doing ... Read more
Energy Absorption Systems, LLC in Pell City has saved over $136,000 in the past eight months by doing ... Read more